Understanding Plasma Table Cutters: Precision Cutting Made Simple
Posted in Industrial Equipment By Ben Eliot On November 26, 2024Plasma table cutters are an essential tool in metalworking, offering unmatched precision and efficiency. Whether you’re a seasoned professional or exploring advanced fabrication techniques, understanding how a plasma table cutter works and its benefits can help elevate your work. These machines are designed to streamline the cutting process for various types of metals, making them invaluable in industries like construction, automotive, and art fabrication.
Here’s an in-depth look at plasma table cutters, their uses, and why they’re a game-changer in modern manufacturing.
What is a Plasma Table Cutter?
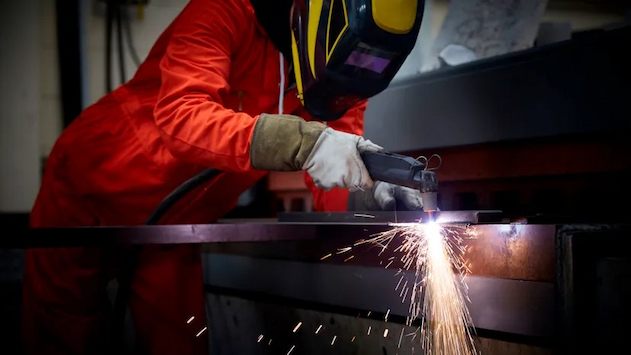
At its core, a plasma table cutter combines plasma cutting technology with a mechanized table setup to deliver precise and efficient cuts. Plasma cutting itself uses ionized gas (plasma) to conduct electricity and generate extreme heat, melting through metal surfaces. The table setup automates and enhances this process, allowing for intricate designs and consistent results.
A plasma table cutter typically consists of:
- A Plasma Torch: This directs the high-temperature plasma to cut through metal.
- CNC Controls: Computer numerical control (CNC) technology guides the plasma torch with precision.
- A Cutting Table: A robust platform that supports the material being cut and collects debris.
How Does It Work?
The process begins with the plasma torch generating a high-velocity stream of ionized gas. This plasma stream reaches temperatures of up to 30,000°C, easily cutting through conductive materials like steel, aluminum, or copper. CNC technology controls the torch’s movement, following pre-programmed designs to ensure accuracy.
What makes plasma table cutters unique is their ability to cut complex shapes with minimal material waste. The CNC system ensures consistency, making it ideal for producing multiple identical parts or highly detailed custom work.
Applications of Plasma Table Cutters
Plasma table cutters are versatile, catering to a wide range of industries. Here are some common applications:
- Industrial Fabrication – Plasma table cutters are widely used in manufacturing plants to create components for machinery, vehicles, and construction projects. Their precision ensures parts fit perfectly, reducing errors and delays.
- Custom Metalwork – Artists and fabricators use plasma cutters to design intricate metal art pieces, decorative panels, and sculptures. The ability to cut detailed shapes makes these machines a favorite in creative industries.
- Automotive Repairs – Plasma cutters are essential in the automotive world for cutting, shaping, or modifying metal parts. They can handle the thin metals used in car panels as well as thicker materials for structural components.
- Construction and Engineering – In construction, plasma table cutters are invaluable for creating structural elements like beams, brackets, and support frames. Their precision ensures safety and durability.
- Prototyping – Engineers and product developers rely on plasma cutters for prototyping. The speed and accuracy of these machines allow for quick iteration during the design phase.
Key Advantages of Plasma Table Cutters
- Precision and Accuracy – The combination of plasma cutting and CNC technology results in highly accurate cuts. This is especially important when dealing with complex designs or tight tolerances.
- Efficiency – Plasma table cutters significantly reduce cutting time compared to traditional methods. This efficiency translates to increased productivity, whether you’re working on small-scale projects or large manufacturing runs.
- Versatility – These machines can cut a variety of conductive materials, including mild steel, stainless steel, aluminum, and more. They also handle a range of thicknesses, making them suitable for diverse applications.
- Cost-Effectiveness – By minimizing material waste and reducing labor time, plasma table cutters offer a cost-efficient solution for metal cutting.
- Ease of Use – Modern plasma table cutters come with user-friendly interfaces, making them accessible even to those with limited CNC experience.
Choosing the Right Plasma Table Cutter
When selecting a plasma table cutter, it’s important to consider your specific needs and the type of projects you’ll be working on. Here are some factors to keep in mind:
- Table Size: Choose a table that accommodates the size of the materials you typically work with. Larger tables are ideal for industrial applications, while smaller ones are sufficient for hobbyists or small workshops.
- Cutting Capacity: Ensure the machine can handle the thickness of the materials you’ll be cutting. Check the specifications for maximum cutting depth.
- CNC Features: Look for advanced features like touchscreens, easy file import options, and precision controls to simplify the cutting process.
- Durability: A sturdy frame and high-quality components will ensure the machine lasts longer and performs reliably under heavy use.
- Support and Maintenance: Opt for a machine from a reputable manufacturer that offers customer support and access to spare parts.
Maintaining Your Plasma Table Cutter
To keep your plasma table cutter performing at its best, regular maintenance is essential. Here are some tips to ensure longevity and efficiency:
- Clean the Table: Remove debris and slag from the cutting table after each use. This prevents buildup and ensures smooth operation.
- Inspect the Torch: Check the plasma torch for wear and tear. Replace consumables like electrodes and nozzles as needed.
- Calibrate Regularly: Ensure the CNC system is properly calibrated to maintain precision.
- Monitor Gas Supply: Use clean, dry air or the appropriate gas for your plasma cutter. Moisture or contaminants can affect performance.
- Check Software Updates: Keep your CNC software updated to take advantage of the latest features and improvements.
Safety Tips for Using Plasma Table Cutters
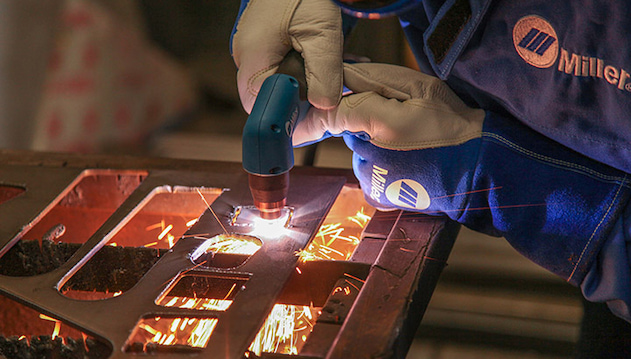
Working with plasma cutters involves high temperatures and electricity, so safety is crucial. Follow these guidelines to stay safe:
- Wear Protective Gear: Use gloves, goggles, and appropriate clothing to protect yourself from sparks and hot metal.
- Ensure Proper Ventilation: Plasma cutting produces fumes that can be hazardous. Work in a well-ventilated area or use fume extraction systems.
- Secure Materials: Make sure the metal being cut is stable and properly secured to the table.
- Follow Electrical Safety: Always follow the manufacturer’s guidelines for electrical connections and grounding.
Conclusion
Plasma table cutters are a cornerstone of modern metalworking, offering precision, versatility, and efficiency. Whether you’re fabricating parts for industrial use or crafting intricate designs, these machines simplify the process and deliver professional results. By understanding their applications, advantages, and maintenance requirements, you can make the most of your plasma cutter and elevate your projects to new heights.
For those looking to explore this technology further, dive into reputable resources or connect with experts to find the right plasma table cutter for your needs. Whether you’re working in a bustling workshop or experimenting in a home garage, a plasma table cutter can revolutionize the way you work with metal.
About Author
ben